Czym smarować oringi?
16.07.2020
Oringi to gumowe pierścienie uszczelniające produkowane z szerokiej gamy elastomerów. W zależności od rodzaju tworzywa, z którego są wykonane, posiadają one różne właściwości oraz przeznaczone są do zastosowań statycznych lub dynamicznych. Okrągły przekrój uszczelek typu O-ring sprawia, że ciśnienie, któremu jest ona poddawana rozchodzi się we wszystkich kierunkach. Zastosowanie uszczelek ma na celu zapewnienie solidnego uszczelnienia między poszczególnymi częściami maszyny. Prawidłowa instalacja oringów zapobiega występowaniu wycieków i awariom urządzenia.
Montaż oringów – Na co zwrócić uwagę?
Niewłaściwy montaż uszczelek może być przyczyną wielu problemów w przyszłości. Stosuj wyłącznie uszczelki o odpowiednim rozmiarze – zbyt małe są podatne na rozerwanie lub pęknięcie, natomiast zbyt duże – nie są w stanie zapewnić właściwej szczelności. Każdy oring ma swoją maksymalną wytrzymałość na rozciąganie. Po jej przekroczeniu dochodzi do pęknięcia lub rozerwania uszczelnienia, dlatego ważne jest, aby unikać nadmiernego jej rozciągania. Podczas montażu uszczelek, aby nie ograniczać ich funkcjonalności, należy je przesuwać na właściwie miejsce, a nie toczyć. Toczenie podczas instalacji może powodować zwijanie się uszczelki, a w konsekwencji doprowadzić np. do wycieku. W celu łatwiejszego montażu oringu we właściwym miejscu, pomocnym i skutecznym rozwiązaniem jest zastosowanie smaru.Dlaczego oringi wymagają smarowania?
Dla uszczelek typu O-ring warto wykonać smarowanie tuż przed ich montażem, chroniąc je przed ścieraniem, ściskaniem lub przecięciem. Smar umożliwia również prawidłowe osadzenie oringu pomiędzy powierzchniami. Cienka warstwa smaru, równomiernie nałożona na oring wypełnia szczeliny i otwory między uszczelką a miejscem montażu, dzięki czemu uszczelka nie zmienia swojego położenia.Korzyści płynące ze smarowania oringów
- smarowanie oringów ułatwia wsunięcie ich na miejsce, zapewniając ścisłe dopasowanie
- zapobiega rozdarciom, przecinaniu, ściskaniu, ścieraniu uszczelek z gumy
- zapobiega wnikaniem zabrudzeń w powierzchnię urządzeń
- uniemożliwia przesuwanie się uszczelek
- zmniejsza siłę potrzebną do montażu oringów
- usprawnia proces instalacji
- zmniejsza ilość awarii
- dodatkowa ochrona, którą zapewnia warstwa środka smarującego
- niezbędny w zastosowaniach pneumatycznych, próżniowych
- chroni przed korozją poszczególne części maszyn
Jak prawidłowo nakładać smar na uszczelki typu oring?
Istnieje wiele sposobów aplikacji środków smarujących na oringi. Najprostszą metodą jest nałożenie go za pomocą palców, dłoni lub pędzla. Innym sposobem jest zanurzenie oringu w pojemniku ze smarem. Bez względu na wybór metody aplikacji, warto pamiętać, aby na całą powierzchnię oringu nałożyć cienką i równą warstwę preparatu. Przed nałożeniem smaru, należy pamiętać o przeprowadzeniu testu zgodności chemicznej. Niektóre składniki zawarte w środku smarującym mogą powodować pęcznienie gumy (np. produkty ropopochodne). Warto sięgać po smary na bazie estrów, które nie dość, że mają doskonałe właściwości minimalizujące tarcie, to ich stosowanie jest bezpieczne dla użytkowników i środowiska.Na co zwrócić uwagę wybierając smar do uszczelek?
Środek smarujący zastosowany w uszczelkach, które mają kontakt z wysokimi temperaturami nie ma możliwości odprowadzania ciepła. Niskie temperatury powodują natomiast usztywnienie się smaru, co w konsekwencji prowadzi do zablokowania się ruchomych elementów. Ważne jest, aby użyty preparat był odporny na zakres temperatur, w których będzie pracował. Istotnym elementem jest również redukcja tarcia, skład chemiczny, kompatybilność z elastomerem, bezpieczeństwo produktu. W zależności od zastosowania uszczelek, smary powinny mieć stałą wodoodporność.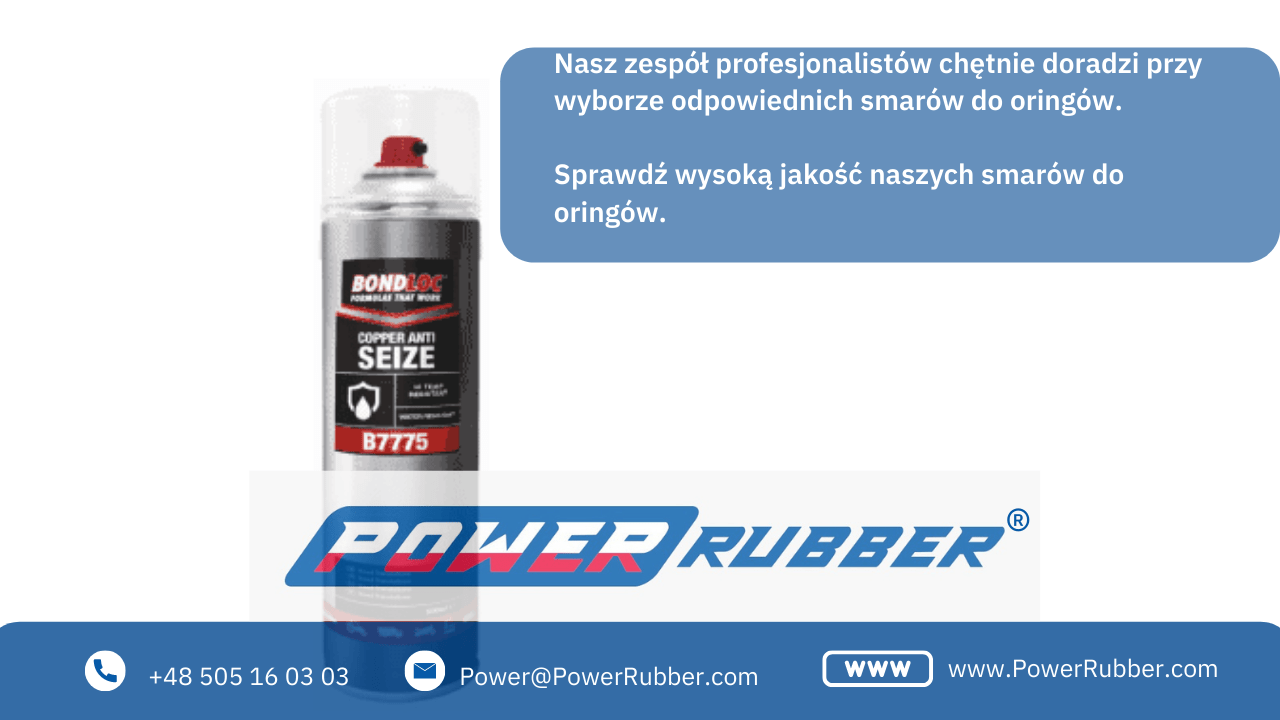
Typy smarów przeznaczone do oringów
Każda substancja smarująca ma za zadanie zminimalizować nagrzewanie i tarcie elementów ruchomych. Jako klient, masz dostęp do wielu rodzajów smarów, które możesz zastosować do szybszego montażu pierścieni gumowych. Dobry środek smarujący minimalizuje współczynnik tarcia, nie powoduje pęcznienia ani warunkowego zmęczenia gumowych uszczelek. Smary występują w postaci płynnej, półpłynnej i stałej. Wszystkie wykonane są z oleju bazowego (70% całego składu), zagęszczacza oraz ulepszaczy, o różnych właściwościach.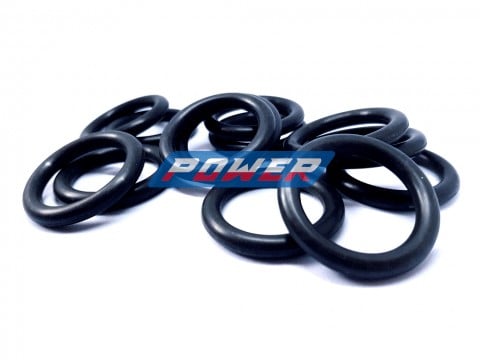
Smar silikonowy
Jest to wodoodporny, nietoksyczny środek smarujący, który chroni przed wilgocią, a także przyśpiesza montaż uszczelek. Cienka, równomiernie rozprowadzona warstwa środka smarującego na uszczelce zmniejsza współczynnik tarcia, wydłużając żywotność urządzenia, w którym jest zamontowana. Smar silikonowy nie plami i nie klei się z kurzem. Wykazuje odporność na utlenianie i parowanie. Może pracować w środowisku o szerokim zakresie temperatur roboczych (od -60° C do +230° C). Zapewnia również dobrą ochronę przed korozją. Dodatkowo może być stosowany w przemyśle spożywczym, w maszynach mających kontakt z żywnością. Silikonowy środek smarujący stosuje się również w urządzeniach sanitarnych (zawory, uszczelki, krany), przemyśle (tekstylnym, papierniczym, motoryzacyjnym).Wazelina techniczna
Wazelina techniczna krótkotrwale zabezpiecza przed korozją. Jest to środek smarujący, który wykazuje odporność na zmienne warunki atmosferyczne oraz wahania temperatur. Stosuje się ją przede wszystkim w nieobciążonych układach w celu ochrony przed tarciem.Smar uniwersalny (litowy)
Preparat wykazuje właściwości hydrofobowe oraz jest odporny na utlenianie i działanie temperatur do 125° C. Wykorzystuje się go w układach pojazdów przemysłowych, rolniczych lub środkach transportu. Zapewnia doskonałe smarowanie podczas intensywnej eksploatacji, chroniąc oringi przed zużyciem oraz wydłużając żywotność łożysk.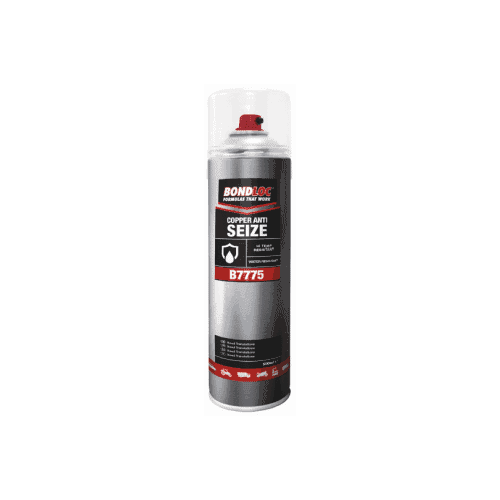
Smar miedziowy
Smary miedzowe wykazują wysoką odporność na działanie wysokich temperaturach (jest nietopliwy) oraz warunków atmosferycznych (deszcz, śnieg). Zastosowanie preparatu zmniejsza zużycie i tarcie, a także chroni połączenia typu metal-metal przed korozją. Powyżej 320° C, ten rodzaj środka smarującego staje się smarem suchym,Smar grafitowy
To środek przeciwzatarciowy o wysokiej odporności na działanie wody. Wykazuje wysoką odporność na obciążenia, pracę w szerokim zakresie temperatur (od -30° C do +600° C) oraz stanowi dobrą ochronę przed korozją. Smary grafitowe stosuje się w elementach narażonych na niekorzystne działanie warunków atmosferycznych, maszynach budowlanych i rolniczych, otwartych przekładniach.Smar bentonitowy
Nietopliwy, hydrofobowy, antykorozyjny, odporny na utlenianie środek smarujący, najczęściej stosowany w aplikacjach pracujących w zakresie temperatur od -40° C do +150° C, w warunkach niewielkich obciążeń, również wewnątrz obudów, które pozostają pod napięciem elektrycznym.Smar molibdenowy
To łatwopompowalny środek smarujący, wyróżniający się wysoką stabilnością temperaturową. Jest odporny na wilgoć, dlatego znajdzie zastosowanie w sprzętach przemysłowych, które pracują w takim środowisku (żurawie, dźwigi), a także w wózkach widłowych lub do smarowania zwrotnic, przegubów. Smary molibdenowe pozwalają również na wyeliminowanie drgań.