Koekstruzja
Koekstruzja to proces łączenia dwóch materiałów w jedną wytłaczaną część. Technologia wytłaczania pozwala na użycie zarówno twardych, jak i miękkich materiałów w tym samym komponencie.
Na czym polega koekstruzja?
Metoda koekstruzji polega na łączeniu kilku odmiennych tworzyw w spójną całość. Formowanie metodą współwytłaczania wymaga użycia dwóch lub większej ilości materiałów do utworzenia określonej części.
W trakcie procesu oba materiały (guma i tworzywo sztuczne) są wytłaczane jednocześnie. W metodzie koekstruzji każdy materiał ma swoją matrycę początkową. Dopiero w dalszym etapie surowiec zostaje przetransportowany do jednej matrycy wytłaczającej, która przed schłodzeniem łączy materiały w jedną strukturę. Następnie w procesie utwardzania (wulkanizacji) następuje trwałe połączenie materiałów.
Ogromną zaletą procesu współwytłaczania jest możliwość łączenia różnych rodzajów gum oraz sztywnych i elastycznych tworzyw sztucznych. Możliwość łączenia różnych surowców pozwala stworzyć produkt, który będzie spełniał różne wymagania funkcjonalne, np. trwałość, elastyczność, odporność chemiczną, odporność na zużycie, wodoodporność i in.
Wytłaczanie kilku warstw jednocześnie sprawia, że mogą się one różnić np. rodzajem użytego materiału, kolorem czy strukturą.
Wybór materiałów uzależniony jest potrzeb i miejsca zastosowania. Komponenty mogą różnić się między sobą uzyskaniem lepszych właściwościami mechanicznych, lepszym radzeniem sobie w określonych warunkach środowiskowych, możliwością recyklingu, dodaniem barwników itp.
Poniżej przedstawiono metodę współwytłaczania w dużym uproszczeniu:
-
Przygotowanie surowców (dodanie barwników, dodatków, inhibitorów UV)
-
Połączenie materiałów
-
Jednorodna mieszanina ulega ogrzaniu i stopnieniu
-
Transport materiału termoplastycznego przez pojedynczą, wspólną głowicę wytłaczającą (matrycę)
-
Następuje proces wulkanizacji (utwardzania)
-
Z połączonych materiałów powstaje wyrób (wytłoczka jest chłodzona)
-
Wyrób jest gotowy do użycia (materiał zachowuje pożądane właściwości, gdy stanie się produktem końcowym)
Ekstruzja czy koekstruzja?
Ekstruzja (wytłaczanie) to rodzaj procesu formowania produktów o ciągłym profilu. W procesie standardowego wytłaczania ciągłe ruchy obrotowe ślimaka wprowadzają surowiec do matrycy, gdzie jednorodna masa ulega formowaniu. Metoda ta używana jest m.in. do produkcji uszczelek do okien i drzwi, profili gumowych, wykładzin, folii.
Koekstruzja różnie się od ekstruzji liczbą tworzyw sztucznych używanych do formowania części warstwowych lub kapsułkowanych. W metodzie koekstruzji używa się dwóch lub większej ilości materiałów. Warto zauważyć, że poszczególne surowce zachowują swoje pierwotne właściwości, ale zostają połączone w jeden komponent. Produkty wykonane tą techniką wymagają zastosowania materiałów, które względem siebie mają odpowiednią przyczepność. Koekstruzję można użyć m.in. do produkcji wysokiej jakości desek kompozytowych na taras, folii LDPE i in.
Warto zwrócić uwagę, że oba procesy wykorzystywane są m.in. przy produkcji desek kompozytowych. W zależności od użytej technologii deski mogą różnić się swoimi właściwościami i trwałością. Przed zakupem należy więc dokładnie zapoznać się ze składem produktu.
W obu metodach powinno korzystać się z wysokiej jakości materiałów. Gorszy gatunkowo surowiec może reagować na czynniki zewnętrzne i tym samym tracić walory jakościowe i estetyczne.
Więcej o procesie wytłaczania tworzyw sztucznych przeczytasz tutaj
Współwytłaczanie - jakie ma zalety?
Podstawową zaletą tego proces technologicznego jest możliwość nadania gotowemu produktowi różnych cech lub pożądanych właściwości. Pozostałe zalety to:
- zastosowanie różnych materiałów zapewnia unikalne właściwości
- każdy materiał zachowuje swoje charakterystyczne, pożądane właściwości (np. sztywność)
- produkcja wielowarstwowa w jednym procesie wytłaczania
- alternatywa do wytwarzania komponentów o wysokiej wydajności
- możliwość zastosowania tańszych materiałów do celów wypełnienia (duże oszczędności)
- opłacalność (duża zawartość surowca może pochodzić z recyklingu)
- zmniejszenie liczby etapów wymaganych w ogólnym procesie wytłaczania
- współwytłaczarki mogą przetwarzać wszystkie materiały termoplastyczne
- obie warstwy tworzą nierozłączne, jednorodne połączenie
- możliwość dodawania różnych wykończeń, kolorów, materiałów do jednego wytłaczanego profilu
- zmniejszenie ilości odpadów związanych z konfiguracją i przycinaniem
Proces współwytłaczania - Zastosowanie
Jedną z zalet współwytłaczania jest możliwość wyprodukowania komponentów o odrębnych właściwościach, które znajdują zastosowanie w różnych sektorach przemysłu. Możliwość przetworzenia wszystkich materiałów termoplastycznych wykorzystywana jest m.in. do produkcji:
-
rurek medycznych
-
profili technicznych
-
płyt
-
blach
-
uszczelek
-
zawiasów
-
opakowań do kontaktu z żywnością
-
współwytłaczania kolorowych pasków na rurach, kablach
- produkcji desek kompozytowych (np. desek tarasowych)
- folia koekstrudowana
W razie jakichkolwiek pytań, zapraszamy do kontaktu pod numerem telefonu: +48 22 292 40 24 lub +48 50 516 03 03, bądź mailowo (power|powerrubber.com| |Power|PowerRubber.com) lub przez nasz formularz kontaktowy
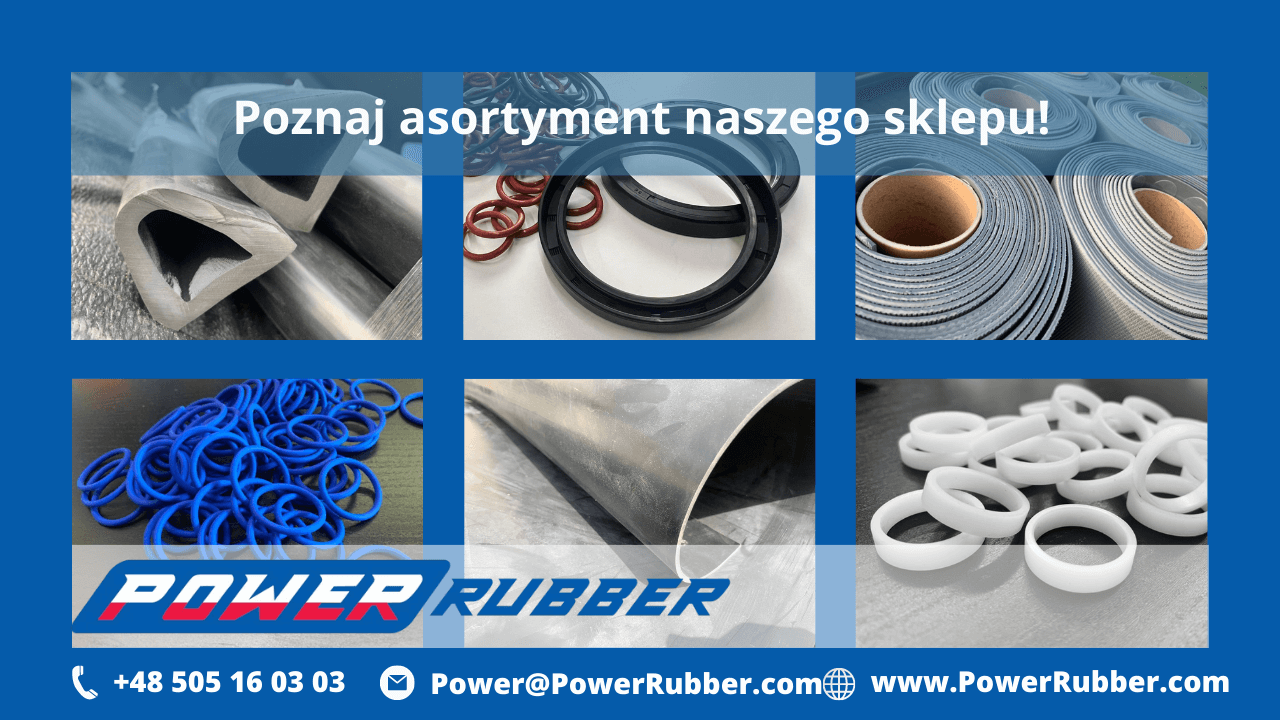
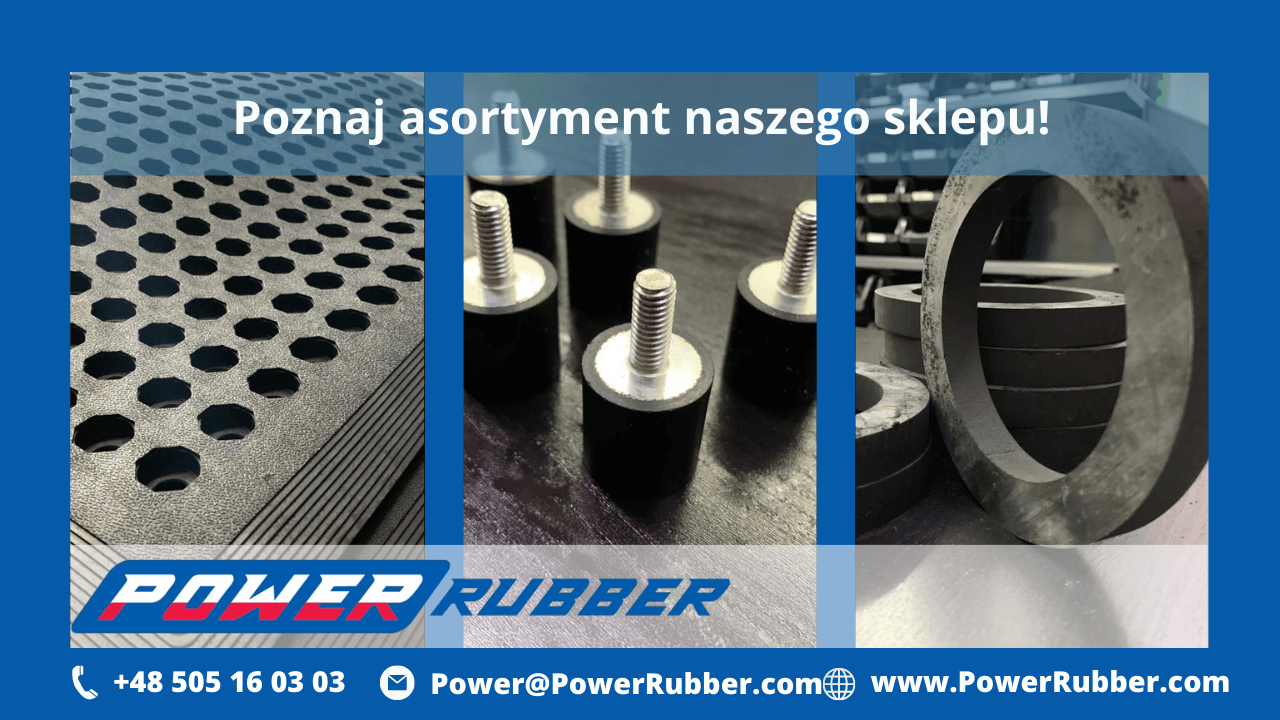
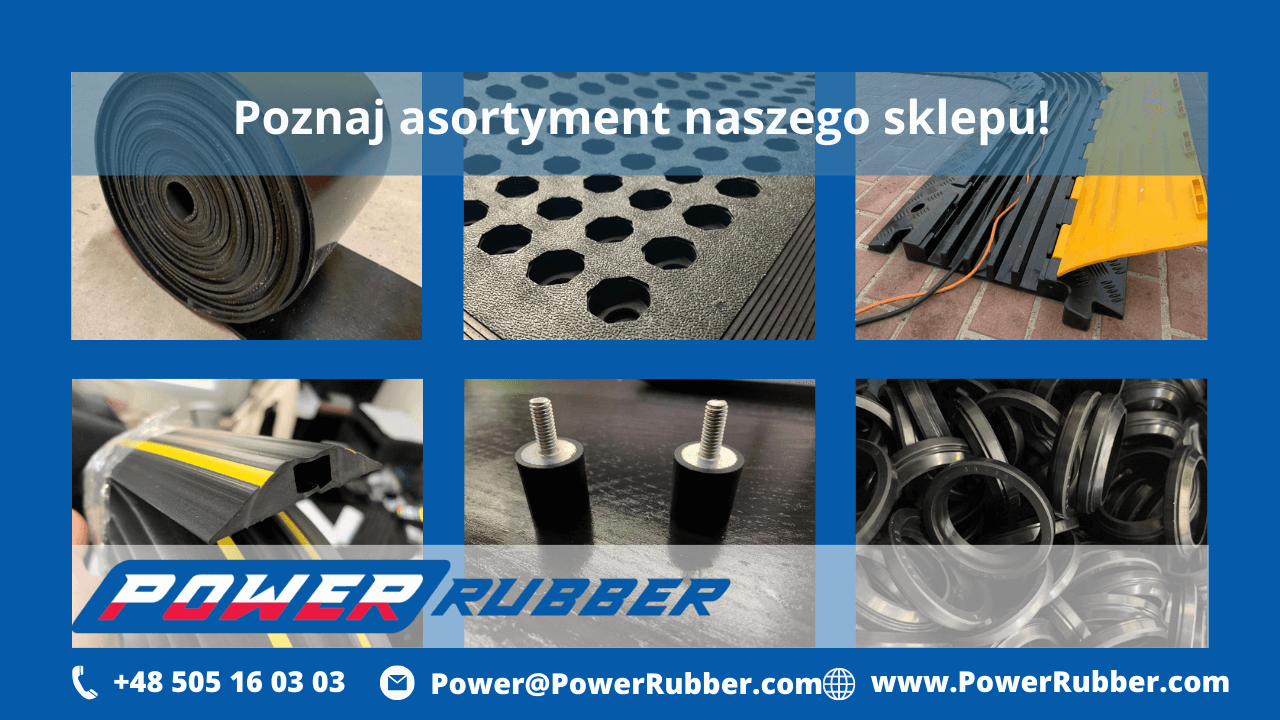
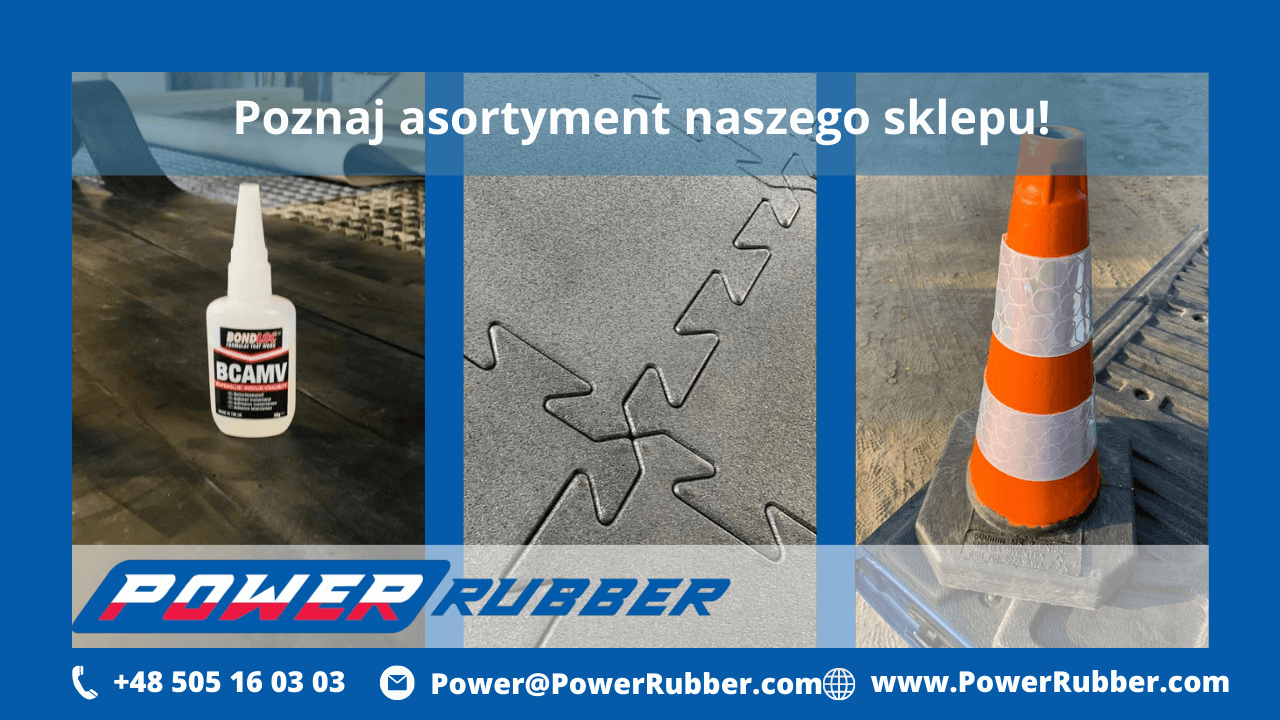
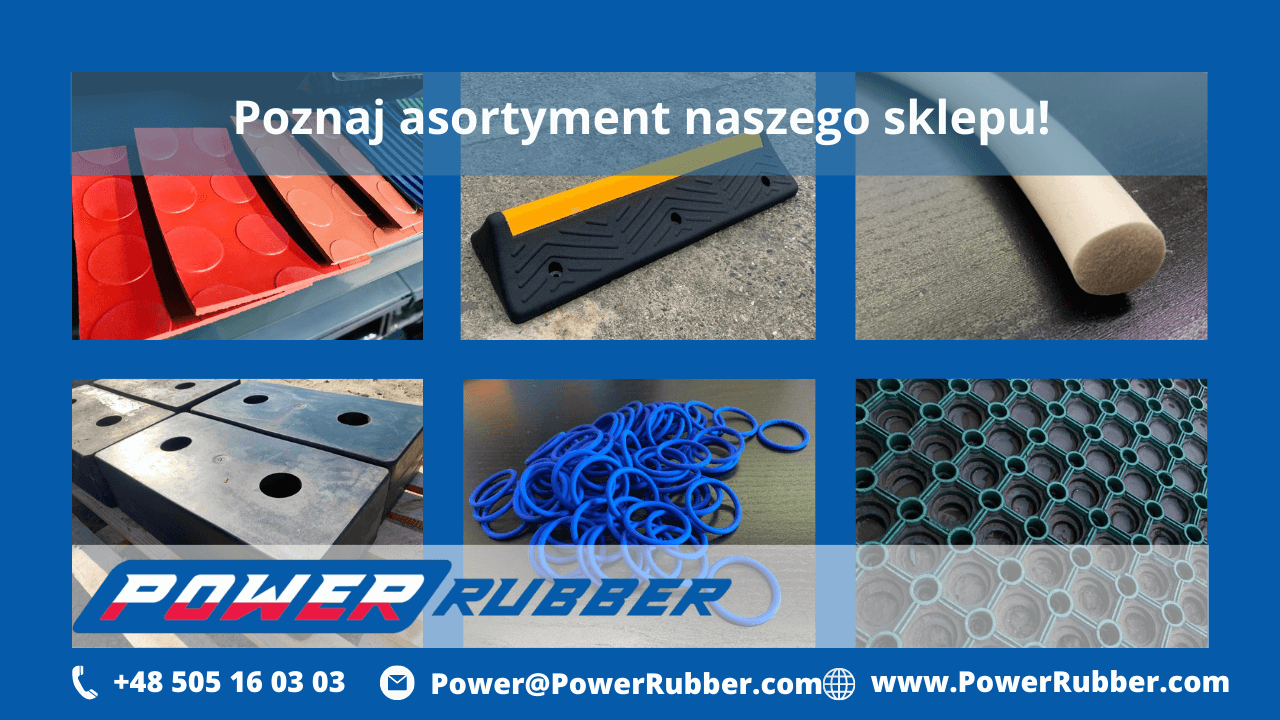