Rubber Coloring
What Is a Colourant Concentrate?
A colourant concentrate is a high-intensity pigment blend in fine powder or granule form, used to colour or enhance polymer properties. In rubber compounds, both organic and inorganic pigments are used—alongside soluble dyes—to achieve vivid, durable rubber colours.
Dyes vs Pigments: Key Differences
Dyes: Natural or synthetic substances soluble in a polymer, creating a transparent colour effect. Common types include basic, acid, direct, and vat dyes.
Pigments: Insoluble colour particles that provide opaque, long-lasting coverage. Available as organic (e.g., chlorophyll or azo pigments) or inorganic (metal oxides, earth pigments). In the UK rubber industry, popular inorganic pigments include:
-
Titanium dioxide (white)
-
Carbon black (black)
-
Zinc yellow (yellow)
-
Cadmium red (red)
-
Chromium green (green)
-
Ochre and copper blues
Choosing the Right Pigment for Rubber
Pigments must be tested to ensure they don’t contain toxic or destabilising impurities. Ideal pigments offer:
-
Excellent UV resistance for long-lasting colour
-
No heavy metals (lead, mercury, cadmium) for food-safe applications
-
Compliance with EU chemical safety standards
Colouring Technology & Sustainable Manufacturing
Rubber processing starts with natural rubber (milky-white) or synthetic base, to which pigments or dyes are added. For example, carbon black not only colours rubber black but also improves tensile strength and abrasion resistance—ideal for high-performance tyres.
Colouring methods:
-
During mix extruding for pellet production
-
Before moulding—using colourant concentrates
Note: The colouring step influences vulcanisation, requiring early addition of pigments and thorough mould cleaning, which can extend production time and costs.
Liquid dyes offer benefits such as uniform colour, thermal stability, environmental friendliness, and consistency in colour application.
Colour Standards and UK-Specific SEO Optimisation
Colourants often follow the RAL colour scale, widely used in industrial settings across the UK. Custom solutions—based on Pantone or sample parts—are available for bespoke requirements.
Summary
Top colouring products for rubber should deliver:
-
High opacity and colour tone
-
Strong UV stability
-
Efficient colouration with minimal usage
-
Good thermal resistance
Poorly mixed pigments may lead to uneven colouring or streaks. To ensure quality, rely on experienced rubber-colour specialists.
For further details, contact us via phone: +48 22 292 40 24 or +48 50 516 03 03, or email: Power@PowerRubber.com.
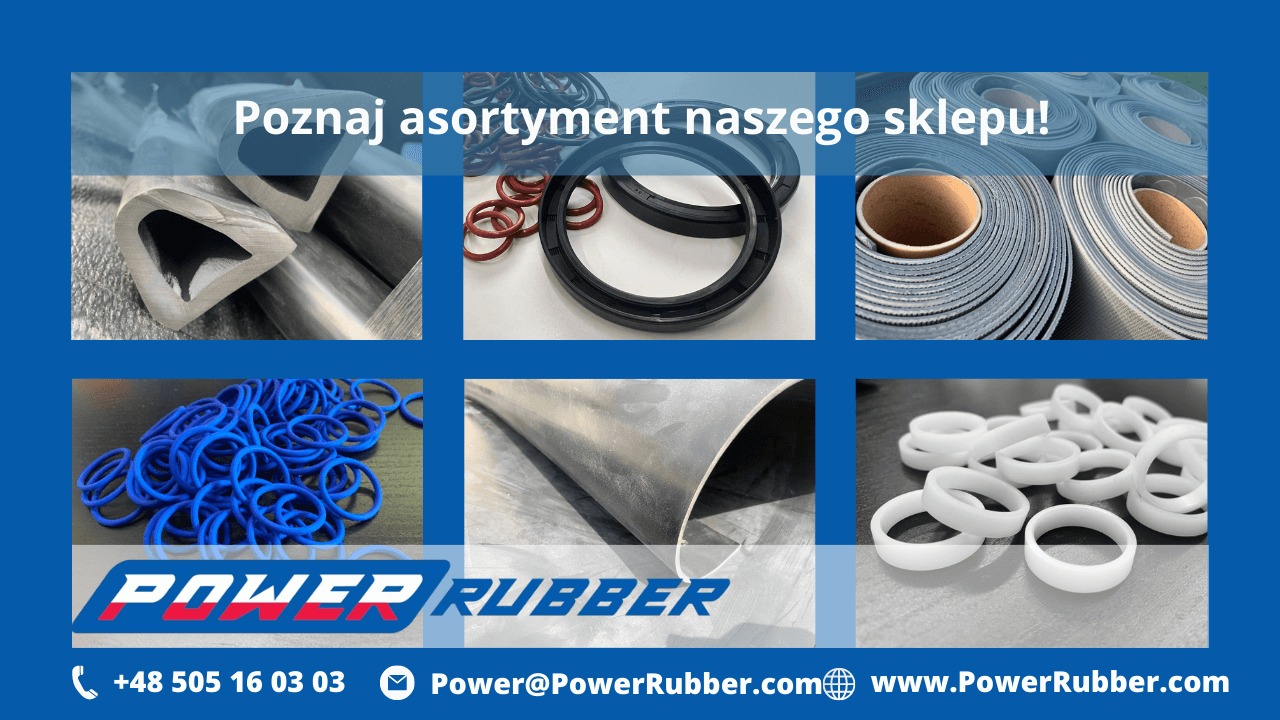
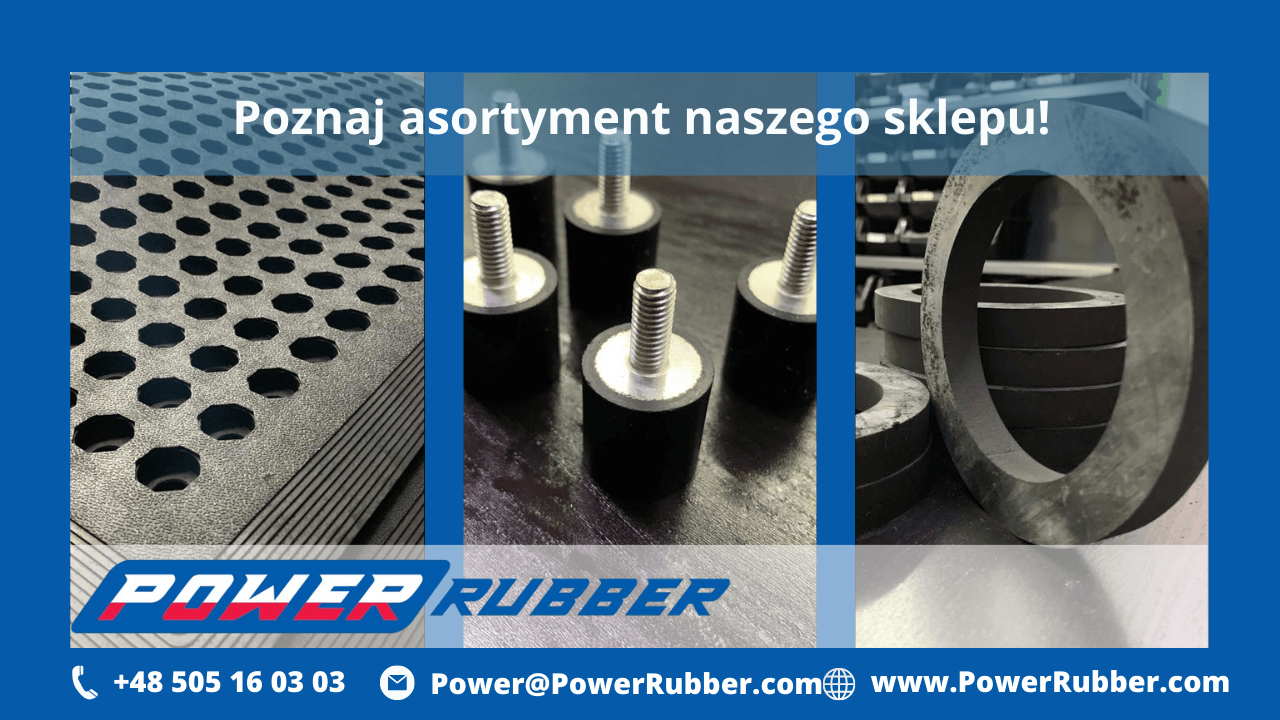
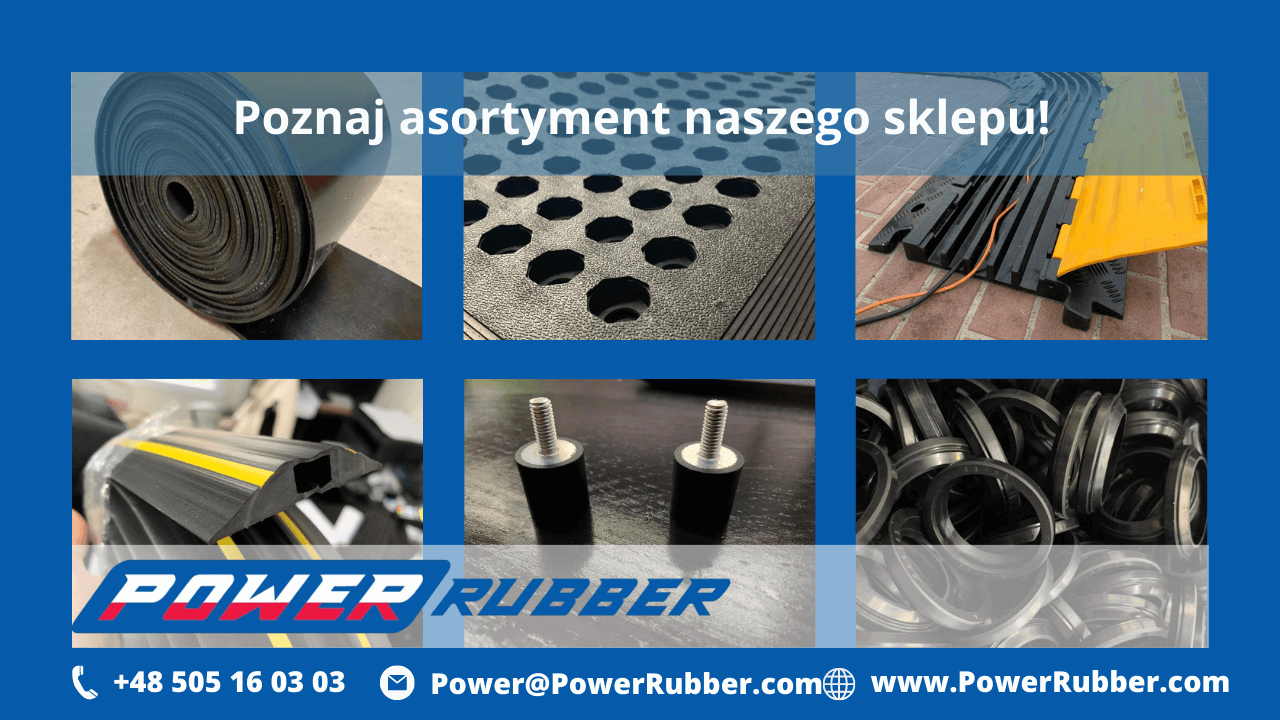
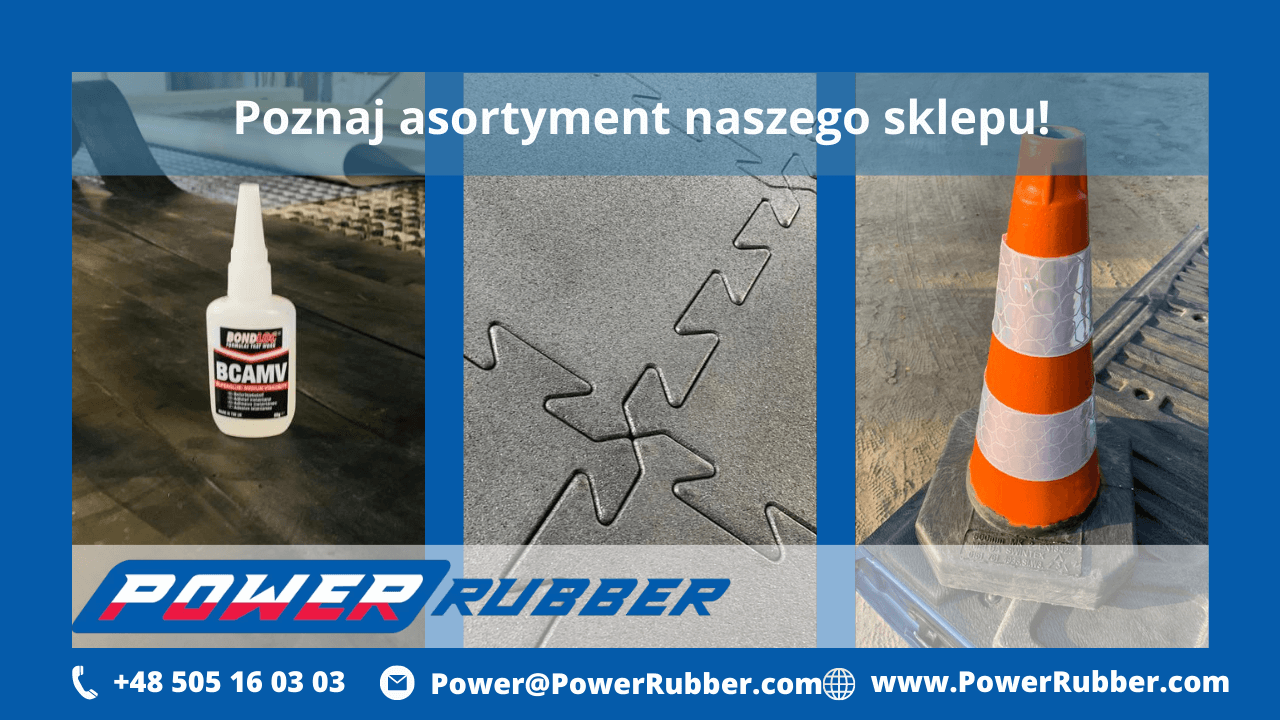
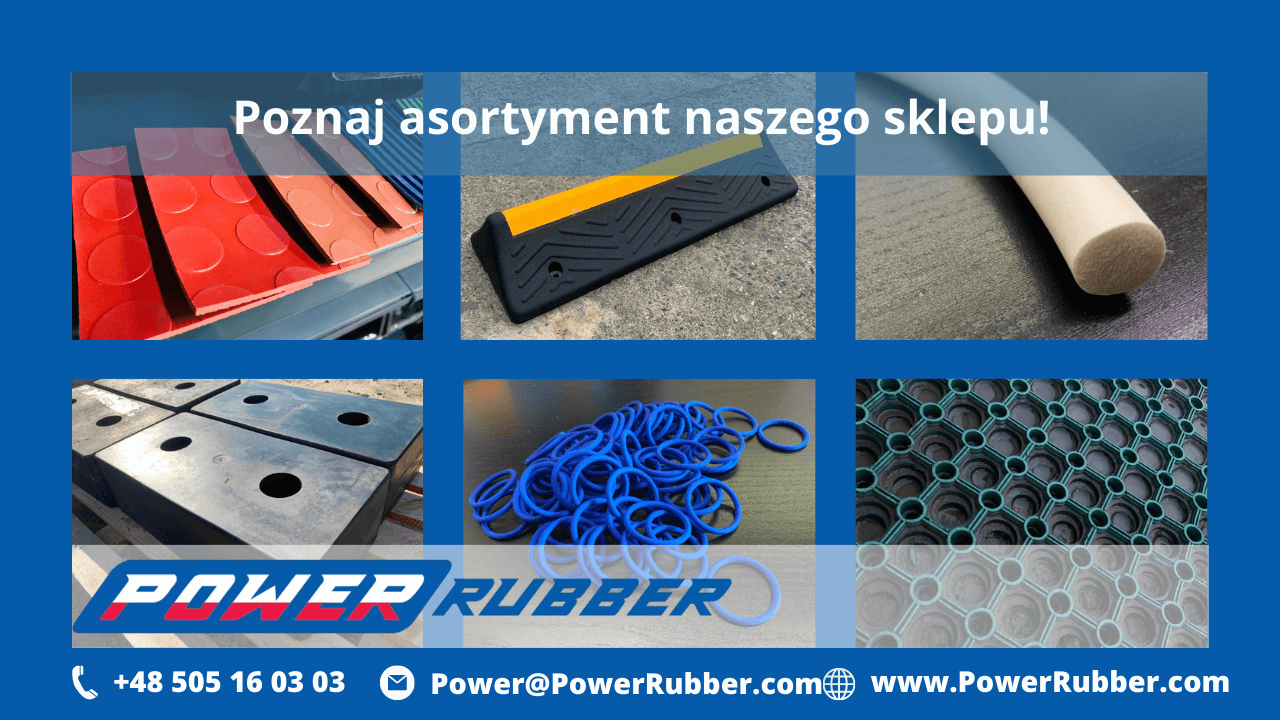