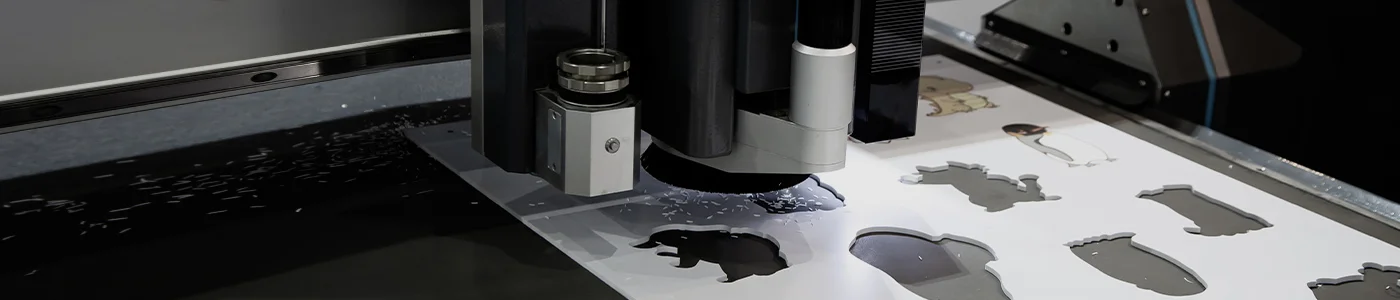
CNC cutting
in Warsaw and surrounding areas at POWER Rubber
The company PowerRubber offers professional CNC cutting services characterized by high precision and versatility. Thanks to advanced technology and modern CNC machines, the company is able to precisely process various materials, both artificial and natural. These services include cutting, milling, cutting, and 3D milling, allowing for the realization of even the most complex projects. PowerRubber specializes in the production of components for various industries. With years of experience and advanced technology, the company guarantees high quality workmanship and timely order fulfillment for both businesses and individual customers.
Contact Form
PowerRubber specializes in manufacturing components for various industries. With many years of experience and advanced technology, the company guarantees high quality workmanship and timely delivery of orders, both for enterprises and individual customers.
Feel free to contact us for a quote.
+48 533 78 78 63
power|powerrubber.com| |power|powerrubber.com
Order fulfillment is carried out with great attention to individual customer needs. The process begins with the customer sending a message with a design, based on which the requirements are detailed. During this phase, the details of the shape and dimensions of the ordered elements are determined, thus avoiding any inaccuracies and errors. After final approval of the project, we proceed to the stage of cutting with CNC plotters, ensuring high precision. Finished products are then shipped on an individually agreed date, allowing us to adapt to the needs of each customer. This approach ensures that each order is carried out with the utmost care and in accordance with the
CNC router cutting is widely used in various industries due to its precision and versatility. In the construction sector, it is used to create intricate structural and decorative components and panels. In the automotive industry, it is used to produce parts and components that require accurate detailing. The furniture industry uses the technology to cut complex shapes in wood, plastic or metal, making it possible to create unique and personalized furniture. In addition, CNC cutting is indispensable in the advertising industry, where precisely crafted logos, lettering and other advertising elements are crucial for visual brand communication. With the ability to work with a wide variety of materials, CNC routers are also widely used in the production of components for the electronics industry, horticulture and many other sectors where accuracy and quality workmanship are a priority.
Cooperation with PowerRubber is a guarantee of the highest quality of services and an individual approach to each customer. The company has a modern machinery park and a team of experienced specialists, which allows the implementation of even the most demanding projects with the highest precision. PowerRubber offers comprehensive services from consultation and technical advice, through accurate design development, to precise execution and timely delivery of finished products. Customers can count on full support at every stage of order processing, which minimizes the risk of errors and ensures compliance with expectations. High quality standards, flexibility and attention to detail make PowerRubber a trusted partner for companies in various industries that value professionalism and reliability.
- Cutting acrylic with a CNC plotter
- Cutting aluminum composite panel with a CNC plotter
- Cutting aluminum with a CNC plotter
- Cutting rubber sheets with a CNC plotter
- Cutting Corian with a CNC router
- Cutting decking board with a CNC machine
- Cutting Dibond with a CNC plotter
- CNC cutting of fibers
- Cutting felt with a CNC plotter
- Cutting foil with a CNC plotter
- Cutting sponge with a CNC plotter
- Cutting the gambit with a CNC plotter
- CNC cutting of rubber
- Cutting hips with a CNC plotter
- Cutting HPL with a CNC plotter
- Cutting cardboard (honeycomb slices) with a CNC plotter.
- Cutting cardboard with a CNC plotter
- Cutting composites with a CNC plotter
- Cutting conglomerate with a CNC plotter
- Cutting cork with a CNC plotter
- CNC cutting of Corian
- Cutting laminate with a CNC plotter
- Cutting of foamed and sponge-like materials with a CNC plotter
- CNC cutting with a PAI plotter
- Cutting PVC (foamed) with a CNC plotter
- Cutting PVC with a CNC plotter
- Cutting PVC with a CNC plotter
- CNC cutting of PET
- Cutting foam with a CNC plotter
- Cutting polyurethane foam with a CNC plotter
- Cutting plexiglass (plexi, plexa) with a CNC plotter
- Cutting rubber sheets with a CNC plotter
- Cutting polymers with a CNC plotter
- Cutting cellular polycarbonate with a CNC plotter
- Cutting polonite with a CNC plotter
- Cutting PVC foam board with a CNC plotter
- Cutting a plotter CNC outline
- Cutting leather with a CNC plotter
- Cutting styrofoam with a CNC plotter
- Cutting styrofoam with a CNC plotter
- Cutting cardboard with a CNC plotter
- Cutting tubond with a CNC plotter
- Cutting plastics with a CNC plotter
- Cutting rubber gaskets with a CNC plotter
- Vinyl cutting with a CNC plotter
- Cutting carbon fiber with a CNC plotter
Glossary of CNC router cutting terms
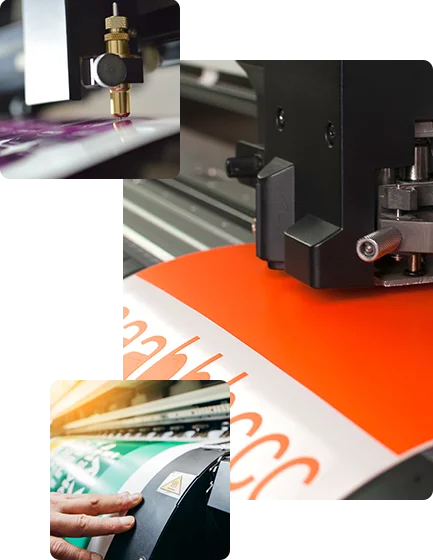
CNC machine service technician
The CNC machine service technician uses his or her theoretical knowledge and experience in machine and equipment construction, as well as the ability to read technical documentation, CNC programs and work instructions to make sure everything is configured according to specifications. Checks the condition of machines using measuring instruments and performs preventive maintenance on CNC machines. Inspects the condition of equipment in accordance with warranty contracts and performs repairs to mechanical defects.
Press brake operator
A press brake operator specializes in managing and operating press brakes. A CNC press brake is a machine tool that is used to precisely bend and shape metal into various forms and shapes during the manufacturing process. A press brake operator has the extensive technical knowledge required to operate complex machines. He or she is responsible for properly setting up and adjusting the machines and controlling the speed, feeding the material, the path of the shape or bend and producing high-quality products. In addition to setting up and operating press brakes, he or she interprets detailed instructions and technical drawings to determine task requirements and the correct manufacturing process. The press brake operator's duties also include quality control, during which he checks the accuracy of bending and performs routine checks. He or she also ensures that finished parts meet specifications and that part production meets schedule requirements.
Automation Specialist
An automation specialist designs, programs, tests and implements technologies to automate machines and processes to perform precise tasks. He or she has expertise in technology and engineering to develop automated and cost-effective solutions that optimize productivity and minimize human intervention.
Spindle
The spindle is an industrial power tool that is a critical part of a CNC machine. It holds and rotates the cutting tool, and provides the necessary power and speed for cutting, shaping or drilling operations during the machining process. It is designed for continuous operation.
The spindle motor is controlled by the CNC machine software. The spindle speed (measured in rpm) can be programmed via the machine interface and can be customized to meet the needs of the machining operation (including specifying the speed, direction and duration of rotation). The CNC spindle provides precise control over speed and torque, which is essential to meet even the most demanding machining requirements.
CNC controller
CNC controller is a computer numerical control device that controls processes and machines. It is responsible for processing, programming and coordinating machine movements. It receives commands from a G-code file containing toolpaths, interprets them and converts them into electrical signals that drive the CNC machine's motors to control its movements.
Treatments
Cavity machining is a type of material processing, in which the process of shaping the workpiece is combined with the need to remove a certain volume of raw material. It is divided into machining and erosion machining.
Machining is a manufacturing process involving the removal of excess material (surplus) using sharp cutting tools to obtain the desired shape and dimension of the workpiece. It is also called cavity machining. Machining, due to its efficiency and precision, has become a standard in many production-oriented industries. It is divided into two groups: chip machining and abrasive machining.
Chip machining is a type of machining that uses tools with a regular geometry and number of blades to remove excess raw material in order to achieve a specific shape and dimensions of the workpiece. Excess material is removed in the form of chips. Chip machining is divided into turning, boring, milling, drilling, chiseling.
Abrasive machining is a type of machining using a wide range of grinding tools of indefinite geometry to remove a small amount of material in order to standardize the dimensions of the workpiece and obtain the desired surface roughness. Excess material is removed in the form of very fine chips and dust using abrasive particles in the form of stone, paste, cloth, paper.
Grinding
Grinding is a type of CNC machining that uses an electrically driven rotating grinding wheel to accurately remove material from the surface of a workpiece. The entire process is controlled and supervised by a CNC system that precisely dictates the movement and speed of the grinding wheel. CNC grinding is the machining method of choice for the most demanding applications where quality and precision are a priority. It provides smooth and uniform surfaces and high dimensional accuracy. This type of machining is characterized by efficiency and high repeatability - the CNC machine repeats the task with high accuracy, which is crucial in mass production.
Reaming
Reaming is the precision machining of an existing hole to finish the surface and precisely increase its diameter to specific dimensions. This CNC machining process involves the use of a multi-tool cutting tool called a reamer, which removes a small amount of material from the surface of the hole. Reaming with a CNC machine tool automates the entire process, which is repeated until the desired diameter and surface finish is achieved. CNC reaming plays an important role in improving the overall quality and performance of workpieces. It improves roughness, offering a smooth surface finish, and improves the accuracy of the hole, which is round, straight and of precise diameter. Reaming is able to meet the needs of high-precision manufacturing.
Drilling
Drilling is a precision CNC machining method that uses computer numerical control to produce or enlarge a circular hole in a stationary workpiece by using a rotating cutting tool or drill bit. Drilling is a common operation in CNC machining, and a CNC machine can accurately position and control the speed of the drill. Drilling technology offers a number of advantages, such as accuracy or the ability to be used in a wide range of materials, from metal to wood and plastic. This machining method also has the advantage of greater repeatability, as computer-controlled units are less prone to error. Drilling is possible by using a special type of drilling machine or by using a lathe or milling machine for this purpose.
Planing
Planing is a cutting method used to remove material from the surface of a workpiece to produce a smooth and flat surface. A CNC planer consists of a long bed that supports the workpiece and a cutting head that contains one or more cutting tools, such as knives or chisels. The cutting head moves back and forth along the bed to remove material from the workpiece.
Computer Aided Manufacturing
Computer-aided manufacturing CAM is software that is used to automate the manufacturing process. It enables efficient and accurate programming, reducing human error and increasing productivity. It converts digital CAD designs into instructions that CNC machines can understand. It's the use of computer software to generate toolpaths and support manufacturing processes. CAM is used to create programs for a variety of CNC machines, such as milling and turning machines, as well as machines for edge machining or additive manufacturing. CAM technology is essential in industries where precision and productivity are paramount.
Computer Aided Engineering
Computer-aided engineering CAE refers to the entire process of manufacturing engineering to design and virtual testing using analytical algorithms, up to production planning. It is used to analyze and optimize designs created in CAD software. It combines CAD computer-aided design with disciplines such as finite element analysis (FEA), computational fluid dynamics (CFD), multi-object dynamics (MDB), thermal analysis, design and product optimization.
Computer Aided Design
Computer Aided Design (CAD) is a key tool for creating complex and precise digital models. It is used to import and create detailed digital files such as 2D drawings and 3D models. Allows rotation at any angle for all views, as well as for inside and outside views. It allows modification, quick visualization, analysis and optimization of the design. It improves the accuracy and efficiency of the design process, allows easy changes to the design, resulting in reduced design time and increased productivity. CAD software is not limited to CNC machining. Engineers, artists, architects also use the program.
Computer Numerical Control
CNC (Computer Numerical Control) stands for computer numerical control. Computer numerical control (CNC) is a technology used in manufacturing processes to automate the control of movement and operation of machines using computer software embedded in tools. It enables precise, accurate and automated control of machining processes, resulting in higher productivity, better quality, repeatability, the ability to make design changes or produce custom parts, and less waste compared to manual machining.
The first phase of the process involves accurately designing the part to be produced using CNC machines. A digital design file is created using CAD (Computer Aided Desing) software and then translated into machine-readable code, usually G-code using CAM (Computer Aided Manufacturing) software. CAM software is used to generate instructions for CNC machines, generating toolpaths that will control the movement and behavior of the CNC machine, cutting tool and workpiece during the manufacturing process.
CNC milling machine
A CNC milling machine is a computer-controlled machine tool designed to remove material from a workpiece to create intricate shapes, profiles, contours. The cutting tool rotates and moves along the surface of the material while the workpiece is securely clamped to the machine table or held by a clamping device. The machine can move the cutting tool in multiple directions to control the cutting process and produce complex and detailed designs with a high level of precision and accuracy. With automated and precise control, CNC milling machines can consistently produce identical parts. They are suitable for rapid prototyping. They minimize waste through precise control of cutting processes. They can operate with minimal human intervention.
CNC lathe
A CNC lathe is a highly automated, high-precision machine tool that uses computer software to control the movement of cutting tools, enabling accurate shaping of workpieces. The machine rotates the workpiece around an axis while the cutting tool remains stationary or moves along programmed paths. It delivers consistent and highly precise results. CNC lathes are ideal for creating cylindrical, conical or spherical shapes. They perform a wide range of operations such as turning, drilling, reaming, threading and more.
Machine tool
A machine tool is a CNC machine that cuts or moves material according to programming on a controller. It is used to shape or machine metal, wood, plastic and many hard materials. It performs operations with high precision, repeatability and speed. Allows production of complex parts in large quantities with a high degree of consistency. Automates tasks in many industries, reducing the need for manual data entry by machine operators. Basic types of machine tools (CNC machines) include: lathes, routers, milling machines, grinders, among others.
CNC programmer
A CNC (Computer Numerical Control) programmer is a person who uses specialized CAD/CAM software and a command writing language (G-code) understood by CNC machines, necessary to generate accurate toolpaths and machining programs. They create and enter instructions into the computer so that it can control CNC machines to perform tasks such as cutting, drilling or milling materials. CNC programmers interpret engineering drawings and CAD models and transform them into the final, physical product. They also select the cutting tools best suited to the specific machining operation and material being machined, and calibrate the machine's parameters so that it operates precisely and accurately. In addition to programming, they constantly monitor and troubleshoot CNC machines, optimizing the machining process, adjusting parameters to increase productivity and maintain product quality standards. CNC programmers work with engineers, machinists and other staff members to ensure smooth production.
CNC operator
A CNC operator is a specialist responsible for operating numerically controlled machines. He is responsible for preparing, starting and monitoring machining processes such as cutting, milling, turning and grinding. Produces machined parts by programming, configuring and supervising CNC machines in operation. Makes adjustments as necessary.
Verifies quality and conformity of manufactured parts to project specifications. Follows safety and quality regulations in accordance with company guidelines and maintains accurate records of CNC machine operation throughout the process. Maintains production and quality logs. The CNC operator inspects work area and machines before and after production, maintains equipment and performs minor repairs.