Oringi in a no-sheathed wrap with FEP/PFA
20.12.2023
Orings in seamless FEP/PFA cover consist of an elastomeric core and a sealed housing made of modified PTFE. The elastomeric core is made of viton synthetic rubber, also called fluorine rubber (FKM) or silicone. EPDM (ethylene-propylene-diene-monomer) material is not used as a core due to heat-related changes during the production process. The core is surrounded by an airtight bezsh coat consisting of FEP (fluorinated propylene ethylene) or PFA (perfluoroalkoxyalcan). FEP and PFA materials are characterized by significant chemical resistance (similar to PTFE), provide reliable sealing. These properties make them similar to the ptfe fluorine polymer (polytettrafluoroethylene). Orings in seamless FEP/PFA housing are designed for static applications.
Orings with a core made of silicone can be bought here from viton here
Orings in closed housing with FEP/PFA – Advantages
Chemical resistance
The material is used for demanding applications with aggressive media (as in the case of PTFE seals with the exception of certain fluorine compounds and alkaline metals). Fep/PFA seamless orings are conducive to applications where the chemical resistance of the elastomer is insufficient. Combining an elastomeric core (provides flexibility) with FEP and PFA materials (they provide chemical resistance) is a better solution than PTFE seals (they do not provide flexibility).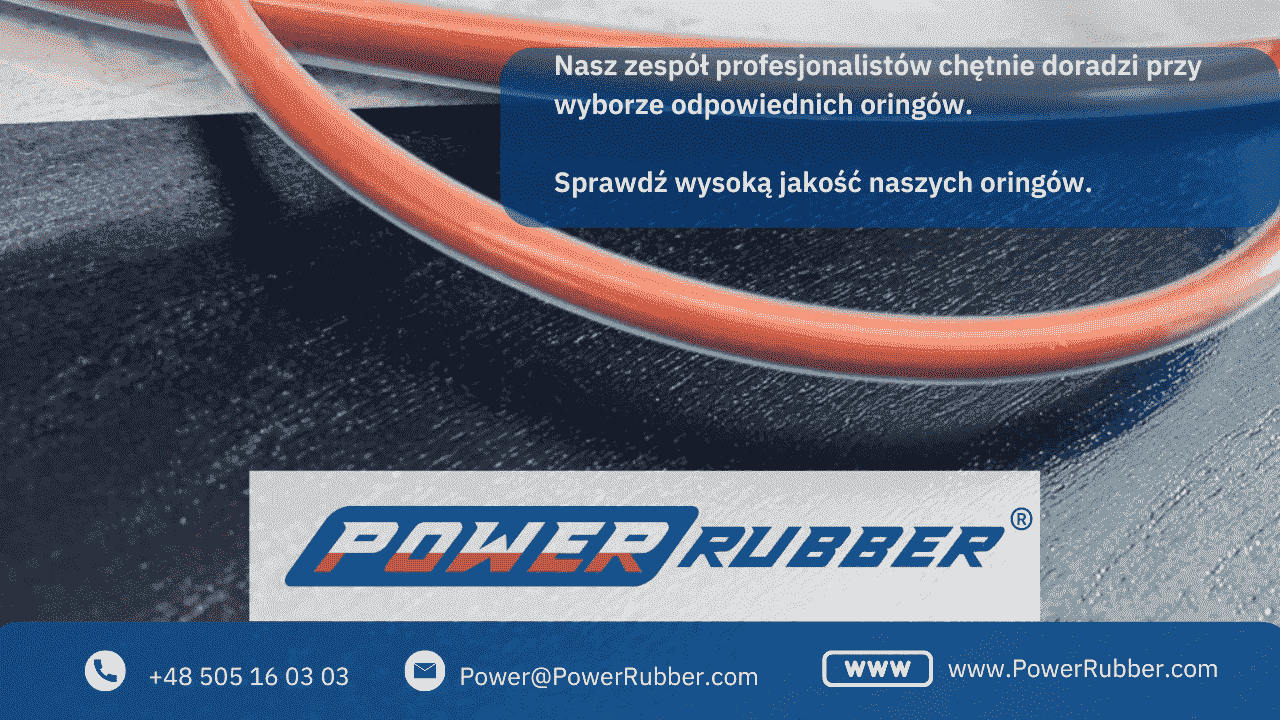
Gas permeability
The PFA and FEP copolymer are high-quality thermoplastics with limited gas permeability. However, compared to other plastics, the penetration of gas through them is significantly lower.Absorption
Orings surrounded by a sealed FEP/PFA jacket are resistant and practically do not absorb (absorb) acids and alkaline. This also applies to elevated temperatures up to 200°C with exposure up to a maximum of 12 months. FEP/PFA material does not absorb solvents at elevated temperatures even if the exposure period is prolonged. Orings in the FEP/PFA enveloping have other properties, i.e.:- resistance to a wide temperature range (temperature range from -60°C to +260°C for pfa silicone core)
- low coefficient of friction (stick resistance, prevents impressive slipping)
- creates very solid seals
Encapsulation (encapsulation) of FEP and PFA
FEP and PFA material have many similar characteristics. PFAs are highly thermally resistant at temperatures above 200°C. The combination of both plastics and core is a combination that is ideal for static applications for m.in. in the chemical, pharmaceutical and food industries. Advantages of FEP encapsulation:- corrosion resistance
- low compression
- high resistance to chemicals
- low coefficient of friction
- corrosion resistance
- high chemical resistance
- low compression
- low coefficient of friction
- increased temperature resistance
- longer service life
- increased mechanical strength
- increased crack resistance
Elastomeric core – advantages
Orings made of fluorine rubber (FKM) and silicone, unlike EPDM, are characterized by high temperature resistance during the production process without any decrease in efficiency. Orings from the FKM core undergoing deformation, show the ability to return to their original form. This is possible thanks to compression. FKM (black) also has good elastic properties. The silicone core is more resistant to temperature than FKM. Silicone core orings are additionally characterized by cold bending flexibility. Pfa and FEP enveloping orings are cost-effective, efficient seals that are ideal for critical applications.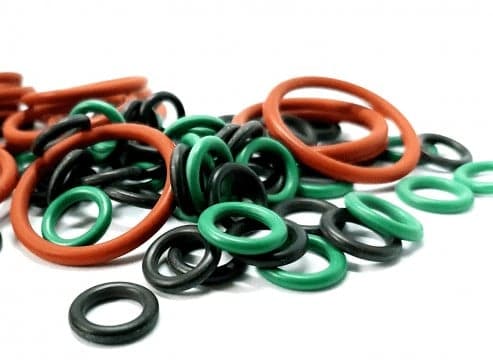
Examples of use of orings in fep/pfa without sheathing:
Fep/PFA orings in a maintenance-free wrap are suitable for static applications thanks to their unique properties:- heat exchangers
- Autoclaves
- mechanical seals
- Filters
- hose seals
- pumps and valves
- gas compressors
- pressure vessels
- tank covers
- relief valves
- Pipelines
- petrochemical industry
- semiconductor production
- Pharmaceuticals
- Chemical
- refrigeration engineering
- Automotive
- Aviation
- food industry
- oil and chemical transport
Comparison with other sealing solutions
There are many types of sealing materials on the market that m.in. promote applications in the chemical industry. Some are chemically resistant and suitable for high temperature applications (e.g. ptfe temperature ranges from -200°C to +260°C). PTFE seals are inert to chemicals (except molten alkaline metals and elemental fluoride). FEP and PFA are distinguished by their resistance to high pressure. Seals made of pure PTFE, on the other hand, are not used in applications that are constantly under pressure. Fep/PFA (PTFE) coated orings are a combination with high PTFE chemical resistance and very good rubber elastic properties.What distinguishes orings in closed FEP/PFA wrap from standard ring seals?
- suitable for static applications
- high chemical resistance (except alkaline metals and certain fluorine molecules)
- wide temperature range
- low pollution
- low coefficient of friction to prevent m.in. uneven movement
- suitable for the use of m.in. in the pharmaceutical, petrochemical and chemical industries
Installation and installation
Proper installation of orings in the wrap guarantees a longer seal life. In case of improper installation and installation errors, the seals may malfunction. To facilitate installation during sealing, place the oring in hot water for 10 minutes and then insert it into the groove. This makes it easier to fit the seal into the case.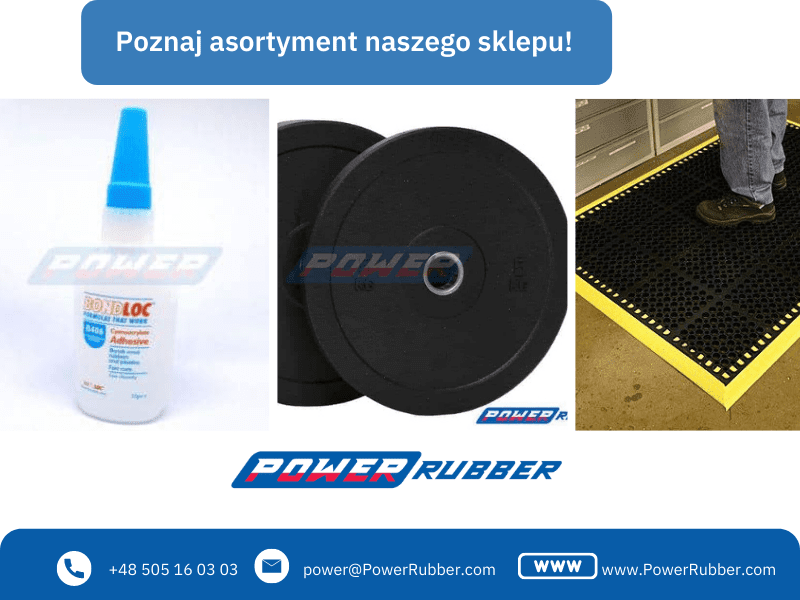