What to lubricate orings?
08.03.2021
Orings are rubber sealing rings produced from a wide range of elastomers. Depending on the type of plastic they are made of, they have different properties and are designed for static or dynamic applications. The circular cross-section of the O-ring seals makes the pressure to which it is subjected spread in all directions. The use of gaskets is aimed at ensuring a solid seal between the different parts of the machine. Proper installation of orings prevents leaks and device failures.
Installation of orings – What to look for?
Improper installation of gaskets can cause many problems in the future. Use only seals of the right size – too small are prone to bursting or cracking, while too large seals are not able to ensure proper tightness. Each oring has its maximum tensile strength. When it is exceeded, the seal ruptures or bursts, so it is important to avoid excessive stretching. When installing gaskets, in order not to limit their functionality, they should be moved to the right place, not roll. Turning during installation can cause the seal to collapse and consequently lead to leakage, for example. For easier installation of oring in the right place, a helpful and effective solution is the use of grease.Why do orings require lubrication?
For O-ring seals, it is worth lubricating them just before installation, protecting them from abrasion, compression or cutting. The grease also allows the oring to be properly seated between the surfaces. A thin layer of grease, evenly applied to the oring, fills the gaps and holes between the seal and the mounting site, so that the seal does not change its position.Benefits of oring lubrication
- lubrication of orings makes it easy to push them into place, ensuring a tight fit
- prevents tearing, cutting, squeezing, abrasion of rubber seals
- prevents dirt from getting into the surface of the equipment
- prevents gaskets from moving
- reduces the force needed for mounting orings
- streamlines the installation process
- reduces the number of failures
- additional protection provided by the lubricant layer
- necessary for pneumatic, vacuum and vacuum applications
- protects against corrosion of individual machine parts
How to apply grease correctly to oring seals?
There are many ways to use lubricants on orings. The simplest method is to apply it with your fingers, hand or brush. Another way is to immerse the oring in a grease container. Regardless of the choice of application method, it is worth remembering to apply a thin and even layer of the preparation to the entire surface of the oring. Before applying grease, be sure to carry out a chemical compatibility test. Some components contained in the lubricant may cause rubber to swell (e.g. petroleum products). It is worth reaching for ester-based lubricants, which not only have excellent properties to minimize friction, their use is safe for users and the environment.What to look for when choosing grease for gaskets?
The lubricant used in gaskets that come into contact with high temperatures is not possible to dissipate heat. Low temperatures, on the other hand, cause the grease to stiffen, which consequently leads to blockage of moving parts. It is important that the product used is resistant to the temperature range at which it will work. An important element is also friction reduction, chemical composition, compatibility with elastomer, product safety. Depending on the use of gaskets, lubricants should have constant water resistance.Lubricant types for orings
Each lubricant is designed to minimize the heating and friction of moving parts. As a customer, you have access to many types of lubricants that you can use for faster installation of rubber rings. A good lubricant minimizes the coefficient of friction, does not cause swelling or conditional fatigue of rubber seals. Lubricants come in liquid, semi-liquid and solid form. All are made of base oil (70% of the total composition), thickening and improvers, with different properties.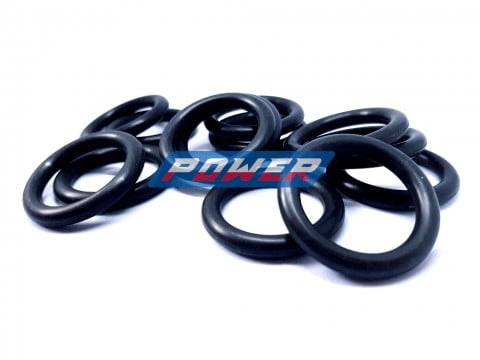
Silicone grease
It is a waterproof, non-toxic lubricant that protects against moisture and also accelerates the installation of gaskets. The thin, evenly distributed layer of lubricant on the seal reduces the coefficient of friction, extending the life of the device in which it is mounted. Silicone grease does not s sta sta stam and does not stick with dust. It is resistant to oxidation and evaporation. It can operate in environments with a wide operating temperature range (-60°C to +230°C). It also provides good corrosion protection. In addition, it can be used in the food industry, in machines in contact with food. Silicone lubricant is also used in sanitary equipment (valves, gaskets, taps), industry (textile, paper, automotive).Technical wazelin
Technical wazelin briefly protects against corrosion. It is a lubricant that is resistant to changing weather conditions and temperature fluctuations. It is mainly used in unloaded systems to protect against friction.Universal grease (lithium)
The preparation has hydrophobic properties and is resistant to oxidation and temperatures up to 125°C. It is used in industrial, agricultural or transport vehicle systems. It provides excellent lubrication during heavy use, protecting orings from wear and extending bearing life.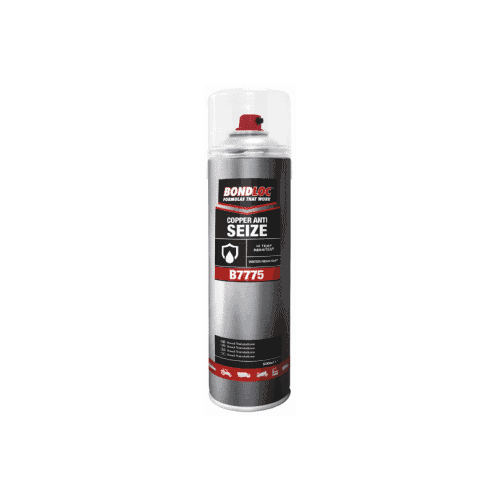